CNC Troubleshooting | A Guide to Resolving Common Issues
- Rt Industrial
- Nov 7, 2024
- 4 min read
Computer Numerical Control (CNC) machines have revolutionized production, allowing precision and overall performance in producing the whole lot from automobile elements to aerospace components. However, like numerous modern-day equipment, CNC structures can come across issues that have an effect on typical overall performance and remarkable. CNC troubleshooting is an essential capability that lets in operators and technicians pick out and remedy the ones problems speedy, decreasing downtime and keeping productiveness.
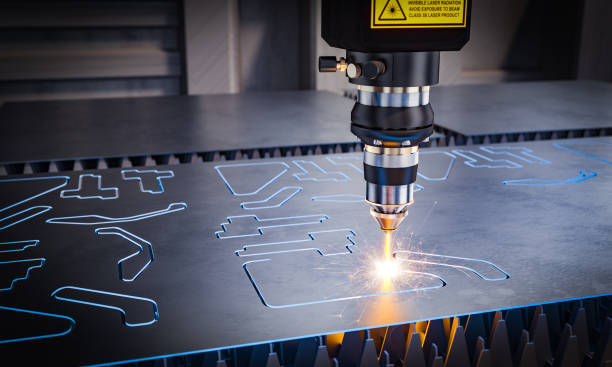
Understanding the Basics of CNC Troubleshooting
Troubleshooting a CNC gadget involves diagnosing troubles with the tool's mechanical, electric powered, or software application additives. It requires a robust facts of CNC operations, a look ahead to element, and familiarity with diagnostic equipment and techniques. Common troubleshooting steps embody:
Observation: Recognizing while some thing is off is the first step in identifying functionality troubles. This could be uncommon sounds, slower processing times, or important inaccuracies inside the final product.
Problem Isolation: Identifying whether or not or not or no longer the trouble lies within the hardware (which consist of the vehicles, axes, or tool head), software (control device or programming mistakes), or environmental factors (like temperature or fabric inconsistencies).
Diagnosis: Using diagnostic tools and software program program utility to pinpoint the correct purpose of the problem. Many CNC machines include integrated diagnostic features to assist operators find out faults.
Testing and Validation: After fixing the problem, walking checks guarantees the device is functioning successfully and that the hassle is genuinely resolved.
Common CNC Machine Issues and Solutions
Here are a number of the maximum common problems that arise with CNC machines and the way to cope with them:
1. Machine Vibrations (Chatter)
Vibrations, often referred to as chatter, are a commonplace hassle in CNC operations. This can rise up due to numerous elements, together with unfastened mechanical components, flawed tooling, or incorrect speeds and feeds.
Solution: Start by using manner of checking free of charge bolts or worn bearings inside the tool’s form. Additionally, ensure the lowering tool is securely hooked up, and alter the rate and feed rate to restrict vibrations. Using a dampening tool or heavier device base can also help soak up vibrations.
2. Positioning and Alignment Errors
Positioning mistakes rise up on the equal time as the device fails to align properly, ensuing in deviations within the very last product’s measurements. This problem can stem from calibration errors, worn additives, or programming faults.
Solution: Calibrate the device frequently to make certain accurate positioning. Inspect the ball screws, guides, and vehicles for wear, as those components play a important role in correct alignment. If positioning mistakes persist, take a look at for software program software program gadget faults or incorrect zeroing of the device axes.
3. Tool Wear and Breakage
Excessive tool positioned on and surprising breakage are commonplace, in particular when managing tough substances or immoderate-amount manufacturing. Dull or damaged tools can reason bad floor finishes, lower accuracy, and increased production fees.
Solution: Schedule regular device inspections and replace or sharpen equipment as important. Optimizing feed charges and speeds for the best cloth being reduce can even growth tool existence. Implementing a device tracking tool that signs and symptoms operators of device put on can lessen the risk of unexpected breakage.
4. Inconsistent Surface Finish
A bad ground give up can prevent end result from incorrect device settings, tired equipment, or wrong lowering parameters. This influences the product’s great and may require extra finishing art work.
Solution: Examine the reducing tool for sharpness and update it if worn. Ensure that the spindle speed and feed charge are because it must be set for the cloth and the popular give up. Also, take a look at for any buildup at the tool, as residue can result in floor imperfections.
5.Control System Errors
Sometimes, the issue lies in the CNC device’s manage gadget, collectively with software program malfunctions, programming errors, or old firmware. Control tool errors can reason the device to function inefficiently or incorrectly.
Solution: Double-check this system for any syntax errors, wrong codes, or records get admission to mistakes. Update the gadget’s firmware and manipulate software program regularly to save you compatibility issues. Consulting the tool’s guide for errors codes or messages also can offer guidance on resolving manage system troubles.
6. Overheating and Cooling Issues
CNC machines generate remarkable warmness all through operation, in particular while operating with metals. Without right enough cooling, overheating can harm components and decrease the device’s lifespan.
Solution: Regularly have a look at the gadget’s cooling tool to make certain it’s functioning correctly. Check for clogged filters or insufficient coolant degrees, and easy or replace those components as desired. Adjusting the feed price and spindle velocity also can additionally lessen warmth buildup.
7. Electrical Issues
Electrical malfunctions, which encompass electricity surges, blown fuses, or defective wiring, can disrupt the CNC machine’s operation or even motive breakdowns.
Solution: Check the electrical connections without fee or damaged wires. Replacing fuses and the usage of surge protectors can prevent damage to the gadget’s electric powered additives. Regular protection tests will help you trap capability electric issues early.
Preventive Maintenance Tips for CNC Machines
Preventive protection is fundamental to reducing the frequency of troubleshooting and maximizing CNC device uptime. Here are a few hints to keep your CNC tool strolling smoothly:
Daily Cleaning: Remove any particles, dust, or steel shavings from the device and the paintings area. This prevents residue buildup that can intervene with device additives.
Lubrication: Regularly lubricate transferring additives at the side of courses, ball screws, and bearings to reduce friction and located on.
Inspect Components: Regularly check out the device’s mechanical and electric components for symptoms of harm, which includes belts, pulleys, and wiring.
Calibration and Alignment: Periodically calibrate and align the tool’s axes to make certain accuracy.
Check Software Updates: Keep the manipulate software software software program and firmware up to date for optimum suitable usual performance and compatibility.
Conclusion
CNC troubleshooting calls for a methodical approach, endurance, and a strong information of the machine’s functions. By learning the way to apprehend and resolve common troubles—like vibration, positioning mistakes, tool placed on, and manipulate device malfunctions—operators can maintain CNC machines taking walks successfully and maintain immoderate requirements of precision. Regular protection and well timed upkeep flow an extended way in minimizing downtime, improving productivity, and increasing the lifestyles of CNC gadget. With those troubleshooting and protection practices, operators can maximize the ability of their CNC machines and make sure consistent terrific in manufacturing.
Comments